Direct-to-Object Printing Equipment: It’s What We Do!
When I tell people that Engineered Printing Solutions builds printing equipment, I usually see a look cross their face as they picture huge offset printing presses with enormous rolls of paper flying through them, like those scenes out of a movie from the golden era of Hollywood that end with a spinning newspaper boldly trumpeting a sensational headline. When I explain that we make printers that print on everything BUT paper, people usually get a confused look on their face. Then I point out the speedometer dial in their car, the branding and instructions on the front panel of their washing machine, or the logo of their favorite football team on the glass they are drinking out of, and I explain that what we specialize in is building “direct-to-object” printing equipment.
Wait, What Is “Direct-to-Object” Printing?
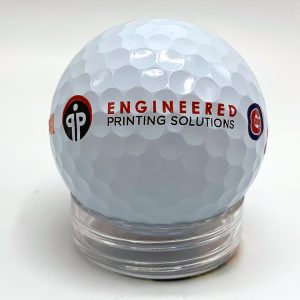
Golf ball printed on a Cylindrical Inkjet Printer
Direct-to-object printing is just what the term implies: printing branding or other decoration directly on three-dimensional objects—everything from drinkware to disc brake rotors to packaging for Consumer Packaged Goods (CPG). More traditional methods of decorating usually focused on printing labels (or, more recently, heat-shrink sleeves in the case of many consumer packaged goods) which were then applied to the product.
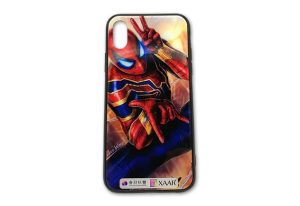
Flat objects such as this cellphone cover present fewer challenges than more 3D shapes.
It should be noted that direct-to-object (DTO) printing is also sometimes referred to as “direct-to-shape” printing. Some people use the term “direct-to-shape” to refer specifically to objects or parts that must be rotated or moved in order to mark all sides of a 3D part, though most people use the terms “direct-to-object” and “direct-to-shape” interchangeably.
Benefits of Direct-to-Object Printing
Direct-to-object printing has several advantages over traditional methods of product-decoration. First and foremost is the elimination of the need to maintain a sufficient inventory of labels (usually printed by a third-party vendor) to prevent production bottlenecks. The addition of labelling machines and label inventories typically requires a greater factory-floor footprint than DTO methods of part-decoration.
By eliminating the dependency on a third-party label supplier, brand owners can rapidly prototype designs, resulting in faster time-to-market for products. Indeed, the rapid changeovers that direct-to-object industrial inkjet printers facilitate not only result in fast prototyping, but they also make extremely short runs economically viable. This opens up a world of possibilities for personalization of products, including versioning and customizing for seasonal and regional variation. Direct-to-object inkjet printers also allow manufacturers to maintain leaner inventories of their products themselves, as they can maintain inventories of semi-finished goods, marking and decorating them “just-in-time” in response to fluctuations in demand along regional or seasonal lines. Leaner inventories also mean less waste of scrap product and unsold inventory.
Finally, direct-to-object industrial inkjet printers such as the ones we build tend to be more environmentally friendly than other methods of product-decoration. Because our direct-to-object printers use solvent-free UV inks and drop-on-demand technology, only enough ink is jetted to mark the part, resulting in very little wasted ink. UV-LED lamps instantly cure the ink to the part, providing durable decoration free from migration and resistant to scratching, peeling, or flaking. Further, the elimination of printing plates and extensive make-ready at the beginning of print runs also contributes to overall savings.
Challenges of Direct-To-Object Printing
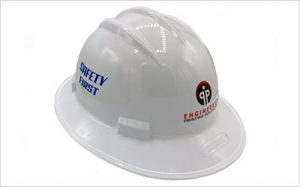
Parts such as this hard hat present a greater challenge, but this helmet was printed on a single pass inkjet printer built by EPS. We have built several hard hat printing solutions over the years.
Direct-to-object printing is not without its challenges, particularly with single pass inkjet printers. Inherently, jetting all the ink necessary in a single pass—hence the name—to create complex designs with subtle gradients and photorealistic imagery on a three-dimensional object moving through space introduces unique challenges. These include, but are not limited to, wind turbulence generated by the movement of the part, the necessity for consistent transport and precise drop placement accuracy.
While the usual solution to this problem is to place the print heads as close to the part as possible (ideally no more than 10mm), most industrial parts have topographical relief in excess of that. At line speeds up to 50 inches per second and higher, ink chemistry and the physical properties of the ink, such as viscosity and shear, must be known and precisely calibrated. For proper adhesion to occur, the surface tension of the substrate must be less than the surface energy of the ink, and to achieve this inline plasma pretreatment is often necessary.
Where a white base layer is applied prior to other colors, UV-LED lamps must instantly “pin” the white ink so that the colors laid down on top do not blend with it. Finally, dedicated software must take into account the precise topography of the part to be printed in order to subtly alter the 2D image to conform to the 3D part and avoid distortion.
More Information on Direct-To-Object Printing
Want to learn more about DTO printing? Download a free copy of our White Paper DIRECT-TO-OBJECT DIGITAL DECORATION: Practical Considerations to find out more.
Or just drop us a line using the form below: